Ultracapacitors
Give Lift to Material Handling
by
Chad Hall, Ioxus, Oneonta,
NY
One
of the most important benefits of ultracapacitors is their ability to
increase the power density of an energy source. Any time a battery is
used to supply power to a variable load, an ultracapacitor can be
used to supplement the primary energy source by increasing its power
density.
Batteries
provide electrical energy by virtue of a chemical reaction, and the
rate of reaction limits the rate at which energy can be delivered.
When a battery is subjected to variable loads, the current draw can
become enormous, causing internal heating that will shorten the
longevity of the battery. However, when an ultracapacitor is
introduced into the equation, this negative effect can be
significantly mitigated.
Lead-acid
batteries are an ideal candidate for combination with an
ultracapacitor bank. A parallel combination of a battery and an
ultracapacitor offers the best of both worlds: high energy density
and high power density. The material handling industry was a natural
avenue for this product, since forklifts are typically powered either
by propane or lead-acid storage battery packs. (For some background
on ultracapacitors and their applications, see “Ultracaps and
Their Uses.”)
The
battery packs used in forklifts are doubly useful. They not only
provide electrical power, they also act as ballast to the forklift,
which is part of the reason they are a popular power source. But in
many large warehouse operations, the batteries have some severe
limitations. It is not uncommon for a forklift operator to deplete a
battery to a level that is inadequate to power the forklift,
requiring a battery swap mid-shift. This situation is exacerbated in
refrigerated warehouse environments—most commonly found in food
distribution centers—because the performance of a lead-acid
storage battery degrades with decreasing temperature.
The
use of a battery pack in parallel with an ultracapacitor bank
provides a power source that will typically last an entire shift.
This battery plus ultracapacitor combination has the added advantage
of increasing the useful life of the lead-acid battery pack. This
latter point is particularly important since prolonging the useful
life of the battery pack represents a significant economic advantage
to the warehouse operator.
The
reasons underlying the improved performance are two fold. First, more
useful energy can be extracted from a battery if it is allowed to
operate within its comfort range. In other words, batteries operate
most efficiently when the current draw is kept moderate. Second, EDLC
capacitor packs have the ability to operate efficiently and without
degradation in low-temperature environments.
In
a typical forklift application, the equipment can draw up to 700 A
from the battery under heavy load conditions. But when the battery is
operating with a parallel EDLC pack, this battery current can be
reduced anywhere from 30 to 45 percent depending on the effective
series resistance (ESR) of the EDLC pack and its interconnecting bus.
The lower the ESR of the EDLC bank and its connecting bus, the
greater the reduction of current drawn from the battery pack.
Due
to the ultracapacitor’s ability to accept fast charges, such as
those in regenerative braking, the additional benefits of energy
harvesting can be used to realize better performance from the energy
storage system. A battery, by contrast, has difficulty with this due
to the chemical reaction rate, which is too slow to absorb the energy
produced in a regenerative braking system.
The
ability of a bank of ultracaps to lessen demands on the battery pack
can be demonstrated with current measurements taken in an actual
forklift application. However, before examining these results, it’s
worth noting the role of control circuitry in the application as this
circuitry plays a role in determining the effectiveness of the
ultracapacitors.
Control
Electronics
The
use of ultracapacitors
often requires
sophisticated control circuits and power electronic circuits for an
efficient and economical application. In an electric forklift
application, the ultracapacitor bank and its associated electronics
must include features necessary for the safe operation of the
forklift, as well as features that maximize the length between
battery charges or changes, and increase the overall battery life.
Specifically, the controller employed in this application must
perform the
following tasks:
Disconnect
the ultracapacitor bank from the power bus in the event the voltage
rises above a preset limit
Disconnect
the ultracapacitor pack when the battery pack is removed for
maintenance
Monitor
current on the power bus and
Engage
the ultracapacitor pack when power is required.
The
controller requirements are designed to protect the ultracapacitor
pack from an overvoltage, which could damage the components; to
incorporate safety LEDs that illuminate to show the ultracapacitor
bank’s charge status; and to ensure the forklift will not
operate from energy stored within the ultracapacitor bank when the
battery pack is not present. This latter requirement is to ensure the
safety of personnel, assuming that when the battery pack is removed,
the forklift will be inoperable. Monitoring the current on the power
bus allows the controller to engage the ultracapacitor bank under
heavy load conditions, which prevents excessive current draw from the
battery pack.
Performance
Data
Measurements
of battery current in an actual forklift application illustrate the
effectiveness of ultracapacitors in reducing current draw from the
battery under load (see the figure). The red trace in the figure
represents the current from the battery without
the ultracapacitor bank engaged. The green trace represents the
current draw with
the ultracapacitor bank engaged. As can be seen from the graph, the
peak current of the battery pack alone is about 750 A and with the
ultracapacitor bank engaged, the peak current is about 550 A or a
reduction of about 25 percent.
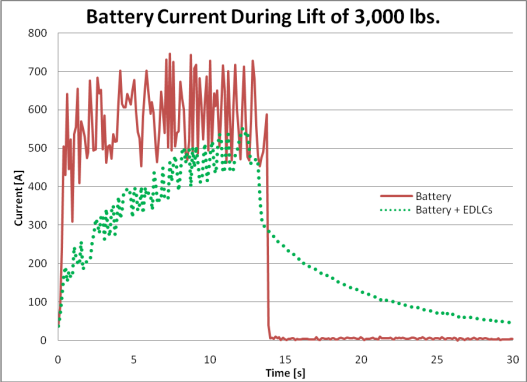
Figure.
Current drawn from battery in forklift application with and without
ultracapacitors (EDLCs).
If
a detailed analysis is carried out, one finds that the reduction in
current drawn from the battery pack depends on the ratio of the
battery’s internal resistance to the effective ESR of the
ultracapacitor bank. The effective ESR includes the ESR of the EDLC
and any additional resistance introduced by the bus and switching
components of the controller that increase the overall series
resistance of the ultracapacitor bank. Therefore, it is important to
minimize the effective ESR of the ultracapacitor bank and control
circuitry.
The
other benefit of reducing the current draw of the battery pack is
that it reduces the damaging effect of deep cycling the lead-acid
storage battery, which is related to the number of charge-discharge
cycles such a battery pack can withstand. Deep cycling a lead-acid
storage battery reduces its effective life. While it is not clear how
long the life is extended (based on the limited data available at
this time), it is clear there is significant extension of the overall
life of the battery pack. Anecdotal data suggests that battery pack
life can be extended by a factor of two to three times, which is
considered a conservative estimate.
Ultracaps
and Their Uses
The
introduction of the first ultracapacitors, or electric double layer
capacitors (EDLCs), by NEC in 1978 ushered in a new generation of
capacitors characterized by energy storage capacities on the order of
a million times greater than conventional capacitors. For example, a
large electrolytic filter capacitor in a power supply might be 5,000
microfarads, as compared to a 5,000-Farad ultracapacitor device that
is readily available today.
The
ultracapacitor market was slow to gain traction because the devices
were initially expensive. The first applications of ultracapacitors
were to supply backup power for volatile memory and internal clocks
in computers, VCRs and other electronic devices. Today,
ultracapacitors are finding their way into power tools, hybrid cars
and public transportation buses, mobile phones and renewable energy
applications. |
About
the author
Currently
serving as chief operating officer of Ioxus, Chad
Hall has used his extensive mechanical engineering and business
experience to take Ioxus from funding to factory to launch.
Chad is responsible for manufacturing and testing of standard
products, as well as further establishing the company and building
the team, increasing sales, locating funding, and spurring continued
product development. Chad is also responsible for educating the
market on Ioxus products and training sales personnel on the
technical aspects of the expanding product line.
Chad spent 14
years with Ioxus’ parent company, Custom Electronics, Inc.
(CEI). In addition, he has been involved in several high-voltage,
high-reliability capacitor projects at national labs. Chad
attended State University of New York, Delhi and received a 3-M
certificate in electro-mechanical design and drafting. Chad is a
member of the American Society of Mechanical Engineers (ASME).
|